Lynx Manual
Overview
- Lynx v1.0
Autonomous, mobile robot (AMR) platform dedicated to an outdoor environment. Compliant with an IP54 or IP66 rate of protection. Depending on the use case, it can be equipped with a robot arm, LIDARs, RGB-D cameras, GNSS receivers, UWB, and other equipment. It can be used in various application areas, such as agriculture, construction, inspection, and many more.
Hardware Guide
Specification
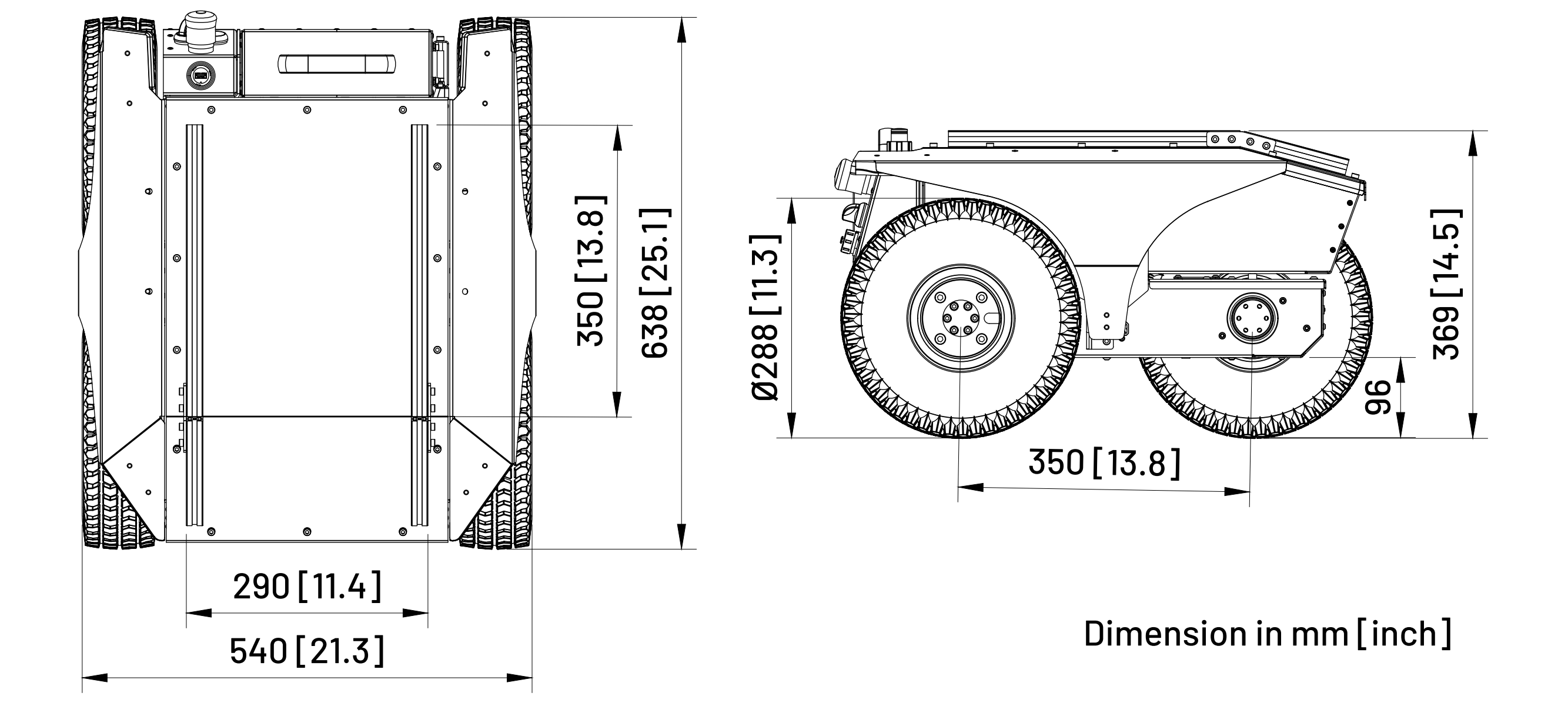
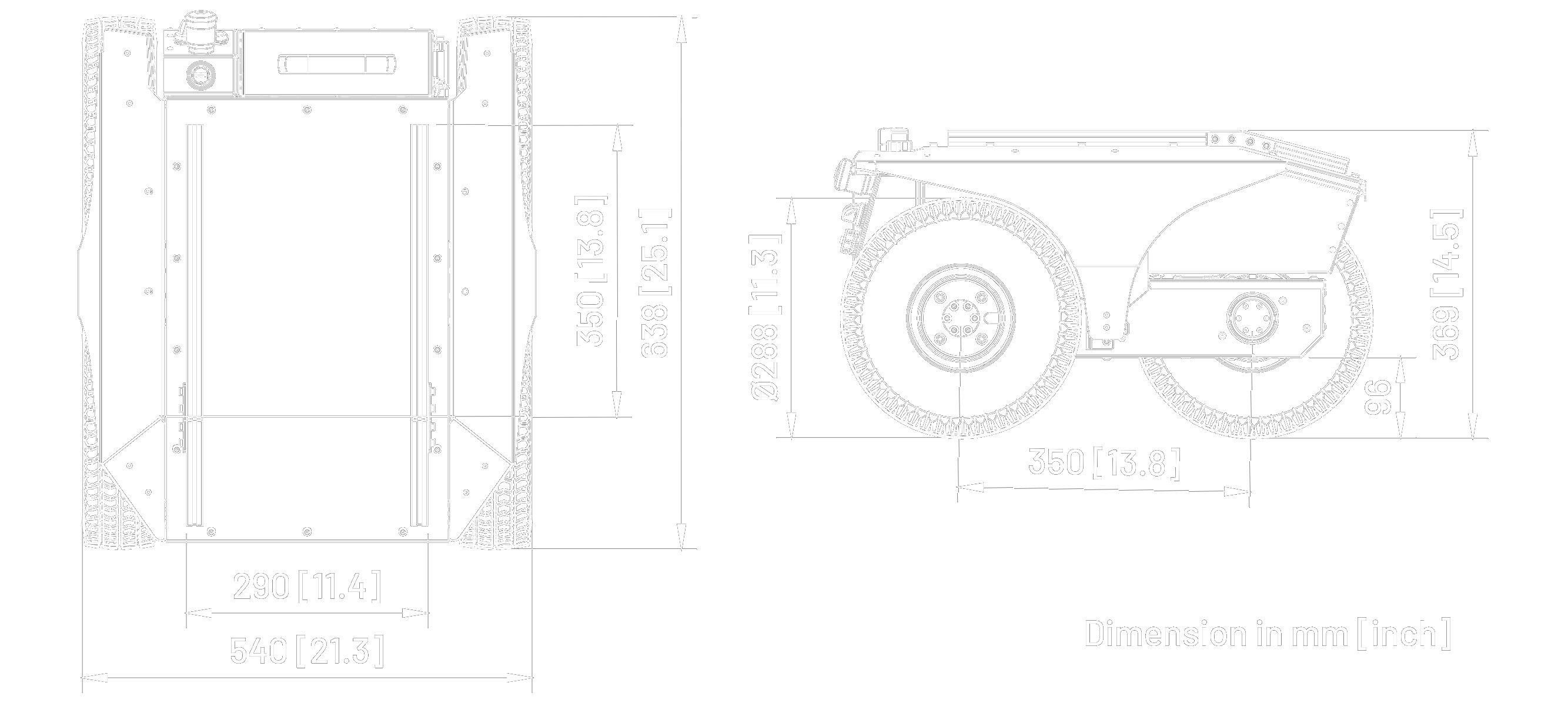
Basic Parameters (with WH05 wheels option)
Name | Value |
---|---|
length | 646 mm |
platform height | 353 mm |
overall height | 373 mm |
wheelbase | 350 mm |
track of wheels | 450 mm |
maximum ground clearance | 90 mm |
minimum ground clearance | 85 mm |
Name | Value |
---|---|
width | 550 mm |
weight | 38.8 kg |
protection index | IP54 / IP66 |
operating temperature | -20°C to 50°C |
storage temperature | -20°C to 50°C |
charging temperature | 0°C to 45°C |
battery type | Li-Ion 36 V |
Traction Parameters (with WH05 wheels)
Name | Value |
---|---|
max speed | 1.5 m/s |
maximum carrying capacity | 65kg |
nominal shaft torque | 34.5 Nm |
maximum shaft torque | 60 Nm |
wheel diameter | 290mm |
payload (cargo) | hill climb grade |
---|---|
0 kg cargo | 90% (42°) |
36 kg cargo | 90% (42°) |
52 kg cargo | 67% (34°) |
65 kg cargo | 56% (29°) |
Great traction, large ramp angles, and high stability are ensured by the low center of gravity, located very close to the center of the robot.
International Protection Rating
The platform is offered in two variants of the protection class. The basic variant is dedicated to moderate indoor and outdoor conditions, with a rating of IP54. The upgraded variant is dedicated to an extremely demanding work environment with a rating of IP66.
Specification of given ratings:
Class | Solid | Fluid |
---|---|---|
IP54 | dust protected | protection against splashes of water from any direction |
IP66 | dust-tight | protection against strong water jets (100 l / min) poured on the housing from any side |
Components
Component | Quantity | Description |
---|---|---|
Built-in Computer | 1 | Quad-core 64-bit SoC @ 1.5GHz and 4GB RAM. Used to manage all the basic functions of a mobile platform. |
User Computer | 1 | ASUS® NUC (Intel® Core i7-1360P, 16GB RAM, 500GB SSD, GPU: Intel® Iris® Xe), Lenovo ThinkStation P360 Tiny (Intel® Core i7-12700T, 16GB RAM, 512GB SSD, GPU: NVIDIA® T1000), or NVIDIA® Jetson Orin NX (ARM® Cortex® A78AE, 16GB RAM, 512GB SSD, GPU: NVIDIA® Ampere) |
Router (optional) | 1 | Teltonika RUTX11 - Dual-band (2.4 GHz / 5 GHz), Access Point / Client Mode, 4G LTE CAT 6, Bluetooth 4.0 LE, GNSS (GPS, GLONASS, BeiDou, Galileo and QZSS) - This multifunctional device ensures reliable external wireless communication and Ethernet link between internal components of the robot system. More details. |
Antenna | 2 | Dual-band (2.4 GHz / 5 GHz) placed on the rear of the robot. |
IMU (Inertial Measurement Unit) | 1 | PhidgetSpatial 3/3/3 Precision (3-axis compass, a 3-axis gyroscope, and a 3-axis accelerometer). More details. |
Fender Lights | 4 | Signal lighting made of APA102C LED chips built into the robot's fenders. |
Brushless Motor with planetary gearbox | 2 | 80PMB800K.80RBL-100 - Drive implemented on 2 durable motors with 473 watts of power (900 W instantaneous power) each and planetary gears with a maximum torque of 60 Nm allows the robot to move at a speed of 1.5 m/s even uphill with a slope of 70% with a load of 40 kg. |
Encoders | 2 | Quadrature, optical encoder, 400cpr (counts per revolution) mounted on the motor. For one revolution of wheels it will count 30*400 = 12000 counts. |
Wheels | 4 | WH05: All-terrain pneumatic wheels. The tire size is 4.00-4. Tire diameter: 288 mm, tire width: 90 mm, rim diameter: 4" |
Additional kits** | Together with the robot, you can get an integrated lidar, depth camera, manipulator, and more. |
Most of the external modules are attached to the profiles on the top of the platform. More details.
Communication
Available as standard
- Ethernet
- USB
Possible to extend
- Wi-Fi (2.4GHz & 5GHz)
- LTE / 5G
- GNSS (including GPS)
- GPS RTK (with PC07 or PC09)
- CAN
- RS232
- RS485
Block Diagram
Graphic representation of Lynx components and connections between them.
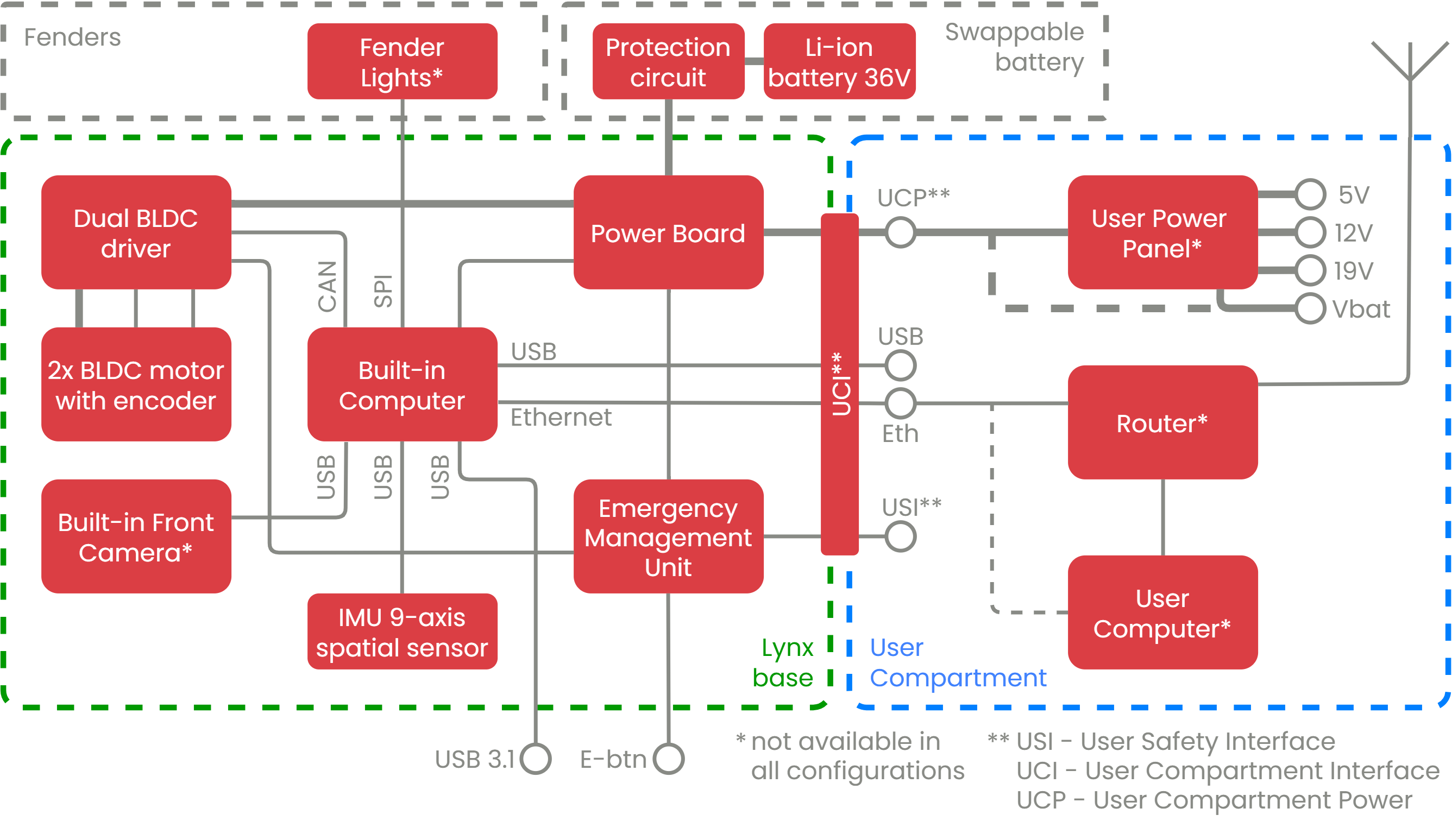
Rear Panel Description
On the Rear Panel of the robot, there are:
- Power controls for the robot - two-position Battery Switch and Power Button.
- USB connection (by default used for Gamepad).
- Emergency Button.
- And the robot's Charging Socket.
Battery Switch
The Battery Switch is used to cut off the Battery voltage from the robot's electrical circuits. Use this switch for long-time storage and shipping. In the event of a robot malfunction, setting the Battery Switch to the OFF position will turn off the robot immediately, without waiting for the operating system to shutdown.
Battery Switch position | Knob position | Power state |
---|---|---|
OFF | left | battery disconnected |
ON | right | battery connected |
Cutting off power using the Battery Switch may cause data loss on the Built-in Computer as well as on User Computers.
Cutting off power by putting the Battery Switch in the OFF position is NOT the same as taking out the Battery. When it is necessary to interfere with the internal components of the robot, it is important to remove the Battery from the robot first!
Power Button and Status LED
Power Button action is triggered with a press and hold of the button for 1 second.
Battery Switch position | Robot status | Power Button action |
---|---|---|
OFF | powered OFF | no action |
ON | powered OFF | power ON |
ON | powered ON | initialize shutdown |
The Power Button is equipped with an LED that indicates the robot's status:
LED state | Status of the robot |
---|---|
ON | powered on |
blinking | shutting down |
OFF | powered off |
When the Power Button is blinking the shutdown process is ongoing. Normally the button should stop blinking after about 10 to 20 seconds. The robot is waiting for the Built-in Computer to indicate a graceful shutdown. In case of an error of Built-in Computer hardware logic will timeout after 140 seconds and cut off the power anyway.
Emergency Button
The Emergency Button is connected directly to the Emergency Management Unit, and it is one of the inputs triggering the E-stop signal. Pushing it runs several actions on the robot. There is a possibility to program the behavior of the platform in emergency situations, however, the default actions are:
- Activate the E-stop signal and latch it.
- Actively brake the robot using motors.
- Toggle an SPDT relay (external E-stop output).
You can read more about the E-stop in the chapter Safety.
USB for Gamepad
There is an USB 3.2 waterproof connector, which provides a direct USB connection to the Built-in Computer. It is dedicated to connecting the Logitech F710 Pad with a modified waterproof USB receiver, but the port can be used to connect any USB 3.2 device to the computer.
Charging Socket
There is a Weipu SP2112/S7 connector mounted on the Rear Deck of the robot with a waterproof cap. The necessary details on charging can be found in the chapter Charging Lynx.
Power Distribution
Battery
The swappable Battery is included with Lynx by default. While purchasing the platform, you can choose the additional, spare Battery, and easily swap the battery if needed.
The Battery packs are made of Lithium-Ion cells with a rated voltage of 36 V and 20 Ah capacity, which gives the Lynx enough energy to move around in demanding terrain and perform calculations for about 4.5 hours. Moving the robot in friendly terrain allows for a significant extension of the robot's working time, up to 9 hours (standby time up to 40 hours).
You can check the battery charge level via the /lynx/battery/battery_status
topic, the WebUI, or by observing the battery charge on Bumper Lights during charging. During normal operation, when the battery level is low (below 40% or 36 volts) or very low (below 10% or 33 volts), the animation will periodically display an orange or red indicator. You can find a preview of the animation in the section dedicated to Animations.
Battery parameter | Value for BAT01 |
---|---|
battery capacity | 720 Wh |
runtime | 4.5 h - 9 h |
standby time | 40 h |
total output power | 1.0 kW |
maximum peak power | 1.8 kW |
Battery Swap
To remove or replace the Battery, you need to unlock one screw.
Be careful not to damage the battery connector seal with the retaining pins pointing out of the Battery. Please do not be surprised of the Battery weight - it is heavy and should be handled carefully. After lowering (1) the Battery to the point when it touches the bottom ledge, slide it towards the connector (2) of the robot and then align it in parallel to the rear side of the robot (3). Then secure with the screw. The bolt holding the Battery in place should be tightened to a torque of 4 Nm. The steps described above are marked in the figure below.
User Power Panel
To meet the user's needs, the robot can optionally be equipped with UPP02 module. It contains 10 high-power electrical connectors that are able to provide a total of 720 W of power to the user's devices.
To meet the user's needs, the robot is equipped with 10 high-current electrical connectors that are able to provide up to 720 W of electrical power to the user's devices. The supply voltages available on the User Power Panel are:
- 5 V limited to 15 A, split into 3x female XT60 connectors,
- 12 V limited to 25 A, split into 3x female XT60 connectors,
- 19 V limited to 10 A, split into 3x female XT60 connectors.
- AUX Power which is the Battery voltage (32 - 42 V) rated at 10 A max. This output is disabled by default. AUX Power can be enabled and disabled separately from the Built-in Computer via a ROS service
/lynx/hardware/aux_power_enable
.
Each of the voltage sources has an independent overcurrent switch, but the total power from 5 V, 12 V, and 19 V outputs is limited to 360 W of power.
Charging Lynx
In the set with the robot, we provide a dedicated Charger, which can charge the robot to 80% in 4 hours, and to 100% in 7 hours. The dedicated Charger can be connected directly to the robot's Charging Socket on its housing. On the top of the Charger, there is a LED indicator. If it is green, that means the Battery is fully charged or not connected. When the LED is red, that means the Battery is charging.
Parameter name | Single Charger |
---|---|
suitable battery options | BAT01 |
input voltage range | 100 - 240 V AC |
input voltage frequency | 50 - 60 Hz |
max output voltage | 42 V |
max output current | 5 A |
It is forbidden to drive the robot during the charging process!
To maintain the long battery life, it is recommended to disconnect the charger after it finishes the charging process (the green LED(s) are ON).
Mounting Rails
Sensors, equipment, and payloads can be attached to the profiles on top of the robot. The profiles used are aluminum T-slot 2020 profiles. The best way to attach the elements to them is to use mounting elements dedicated to this type of profile, such as T-nuts, fittings, and angles.
These profiles are fixed to the top side of the User Compartment. You can remove these together with the User Compartment Cover, or separately.
They Mounting rails may not be available if you ordered the robot without the User Compartment. In this case you can use the User Compartment Mounting Points to secure your own equipment.
The presence of the Mounting Rails on the User Compartment has no effect on the water and dust resistance of the robot.
Fender Lights
Four Fender Lights are assembled to Fenders on the robot's corners. By default, the signaling lighting is mounted on each Bumper in the form of aluminum profiles with 46 programmable RGB LEDs.
These lights contains programmable RGB LEDs and may be widely used to indicate the status of the robot: the direction of movement or the intention to change direction, warn about low Battery charge or other detected errors, signal the status of the charging process, or even to illuminate the area in front of the robot.
User Compartment Interface
On the rear side of the robot, there is an electrical panel called User Compartment Interface. It is designed to provide power and communication to the User Compartment (UC) when it is installed. If not, you can still use this interface for your equipment.
The User Compartment Interface connectors:
- UC Power Connector
- User Safety Interface (USI)
- USB connector
- Ethernet connector
CAD Models
To facilitate the work with the project based on the Lynx platform, we have prepared CAD models for download in three extension formats:
- STEP High Detail - contains a complete model with regular wheels, highly detailed.
- STEP Low Detail - contains a model with limited details.
- STL Low Detail - contains mesh model with regular wheels.
- URDF - The package contains URDF files responsible for creating a representation of the robots using mesh models.
Software Guide
The Lynx UGV’s ROS 2 driver runs on a Built-in Computer powered by a customized Ubuntu-based operating system with a real-time kernel.
Interaction with Lynx's hardware is primarily facilitated through the Robot Operating System (ROS), with all drivers developed in ROS. The source code is available in the GitHub repository husarion/husarion_ugv_ros.
User-level ROS 2 software is intended to run on a separate user computer.
ROS is a set of software libraries and tools for building robot applications, offering a common framework for development. It is open-source, making it free to use and modify.
Software Resources
- ROS 2 API - Learn about the robot API.
- Robot Management and Configuration - Tools and information for robot configuration during development.
- ROS 2 Packages Overview - Detailed information on individual packages.
By default, Lynx ROS is deployed using Docker, which simplifies deployment, management, and updates of the ROS system. While the default setup is within a Docker container, you can run Lynx ROS drivers natively. Instructions are available on the husarion_ugv_ros GitHub page.
Natively built ROS packages do not include autostart functionality. Users need to add it, for example, by creating a systemd service.
The provided Lynx ROS system is designed to compose all the basic functionalities of the robot. It allows to control of the robot with velocity commands and provides the user with odometry information, which can be used for robot localization. The Lynx ROS system is also designed to monitor the robot's state and perform safety features that will prevent any hazardous behavior. The basic states of the robot are represented by the Bumper LED Animations. This allows the user to recognize if the robot is ready to operate or in E-stop mode, informs about the Battery state, or displays an animation indicating the occurrence of an error in the system. More detailed information about the state of the robot can be acquired using ROS topics. Errors in the system are also logged into the system and can be easily accessed using the Docker interface. The Lynx ROS system includes a robot description, which can be used to visualize the robot with all its components.
The Lynx ROS system is designed to be easy to use and maintain. It is also designed to be extensible so that it can be easily customized for different applications.
Launch System Analysis
This section provides an overview of the system launch times for the Lynx robot version 1.0, ROS driver version 2.3.0, and RUTX11 firmware version RUTX_R_00.07.13.3. The measurements were conducted multiple times to ensure accuracy, and the results presented are averaged values.
Autonomy reference stack
The husarion-ugv-autonomy
template repository provides a Docker-Compose workspace that bundles all navigation-related nodes (Nav2), SLAM and the docking server required by Panther / Lynx.
Path | Purpose |
---|---|
compose.hardware.yaml | Launches navigation and docking containers on the real robot. Environment variables such as OBSERVATION_TOPIC , OBSERVATION_TOPIC_TYPE , CAMERA_* and SLAM are forwarded so you can point the stack at any LIDAR/camera without editing the file. Networking is set to host for zero-conf DDS discovery. |
compose.simulation.yaml | Adds a Gazebo container plus a components.yaml model layout. use_sim_time is preset, so clocks are synchronised automatically. |
config/ | Holds runtime parameters: nav2_params.yaml , pc2ls_params.yaml (planner, controller & point-cloud-to-laser tuning), components.yaml (where each sensor is mounted in simulation), docking_server.yaml , apriltag.yaml (dock poses and tag size) cyclonedds.xml (DDS QoS / discovery options) |
sensors/ | Optional compose fragments for bespoke drivers; drop in another file when the default containers do not cover your sensor. |
Helper commands (Justfile)
just dock DOCK_NAME # Dock Husarion UGV to the charging dock using navigation stack
just dock-direct DOCK_NAME # Dock Husarion UGV to the charging dock without using navigation stack
just start-hardware # Start navigation on User Computer inside Husarion UGV
just start-simulation # Start Gazebo simulator with navigation stack
just start-visualization # Configure and run Husarion WebUI
just stop-visualization # Stop Husarion WebUI
just undock # Undock Husarion UGV from the charging dock
Upstream ROS 2 code
Both navigation and docking containers are built from the husarion/husarion-ugv-autonomy:<distro>-<tag>
image, which in turn packages the sources in husarion_ugv_autonomy_ros
(SLAM, Nav2 bring-up, docking state-machine). Fork that repository if you need to change node logic and rebuild the image locally.
Sensor interface
The stack is sensor-agnostic: any device that publishes LaserScan
or PointCloud2
(plus a TF to base_link
) and any RGB-D/mono camera that publishes Image
+ CameraInfo
can be used. Simply export the five environment variables listed in the README, or add a new service under sensors/
that runs your proprietary driver.
Extended notes
A detailed explanation of the architecture and customisation workflow is available in the blog post: https://husarion.com/blog/husarion-ugv-autonomy/
RUTX11
Description | Time (mm:ss) |
---|---|
LAN network availability. | 1:15 |
Wi-Fi network availability. | 1:20 |
Built-in Computer
Description | Time (mm:ss) |
---|---|
Full boot time (from pressing the robot's power button to full system readiness). | 1:18 |
Boot time for RPi | 0:28 |
Time from RPi boot to full system readiness. | 0:50 |
Driver docker container startup time (from RPi boot). | 0:34 |
Driver initialization time inside Docker. | 0:16 |
Safety
The robot has been equipped with solutions for the safe use of the equipment, both in the software and hardware layer.
Please take this chapter seriously. Inadequate and irresponsible using of the robot may cause damage to the device, the workplace, and people in the vicinity.
The robot is equipped with an Emergency Management (EMU). It is a system that takes control of the robot's components as well as its power in crisis situations. The EMU can stop the robot's movement, turn off the power of the user's device, or even turn off the entire robot if so configured. It also provides a dedicated electrical User Safety Interface (USI) led out to the User Space.
Due to the appearance of any trigger, such as a Built-in Computer's CPU crash or Emergency Button press, the EMU will call and latch the E-stop signal. This means that in such situations, for the further work of the robot, the problem should be resolved, and then the E-stop latch should be reset.
This chapter describes only the basic default EMU configuration, however, the system is configurable. To learn more about the possibilities and how to configure them, visit a separate article: Emergency Management Unit.
Hardware
Emergency Button
On the rear side of the robot, there is a red push button. Pushing the Emergency Button causes:
- activate the E-stop signal and latch it,
- actively brake the robot using motors,
- toggle a SPDT relay (external E-stop output).
These actions are the default EMU configuration. To learn more about the possibilities and how to configure it, visit a separate article: Emergency Management Unit
User Safety Interface (USI)
USI is an electrical hardware interface for EMU designed to integrate Lynx with the user's equipment.
Transporting Lynx
Lynx is shipped in a wooden box for two reasons: to protect the robot itself, and to comply with transportation safety regulations for batteries. Li-Ion batteries with a capacity of over 100 Wh are considered dangerous goods. As long as the product with such a battery is properly packaged and marked, it can be transported by various means, including air transport.
If you consider transporting Panther to a remote location, we recommend that you keep the wooden box with the UN3481 marking and Class 9 (batteries) symbol. You will also need to confirm with your carrier that you are working with dangerous goods. For more details, please contact us at support@husarion.com
Before shipping, disarm Lynx by setting all switches to the OFF position and pressing the Emergency Button. Also, the Battery charge level should be below 30%. For air transport keep tires pressure at about 1.5 bar.